The Role of a Heat Press When Using a Direct-to-Film Printer
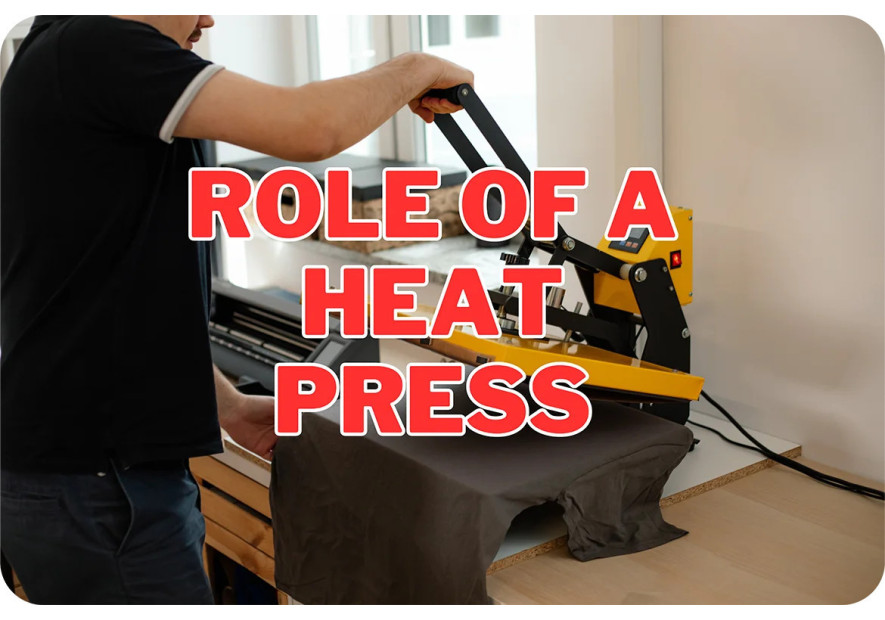
The Role of a Heat Press When Using a Direct-to-Film Printer
How do intricate designs and vivid colors find their way onto a myriad of products with precision and durability? The secret lies in the advanced technology of a direct-to-film printer. However, there is another device that aids in the process: the heat press machine.
At DTF Transfers Wholesale, we specialize in bringing this cutting-edge technology to the forefront of the industry. Our mission is to empower businesses to unlock their creative potential and deliver products that stand out in the competitive market.
Let's explore how the heat press, an essential cog in the wheel, makes all the difference in producing superior-quality transfers.
The Significance of a Heat Press in DTF Printing
In the world of direct-to-film (DTF) printing, a heat press is the key player that turns visions into tangible, high-quality products. Understanding and leveraging the power of a heat press can make all the difference.
Before any design materializes on a product, the pre-printing process lays the groundwork. Here, businesses prepare the design and print it onto a special film.
Next comes the application of hot melt powder, which acts as the adhesive. This stage is critical, and the heat press machine plays a starring role.
After preparing the film with the design and adhesive powder, the heat press machine steps in. It applies the necessary heat and pressure, activating the hot melt powder. This action melts the powder, bonding the design to the product.
For those dealing with large volumes, the consistency and efficiency of a heat press are invaluable. It ensures that each product, from the first to the thousandth, meets high-quality standards.
In DTF printing, the heat press does more than just apply designs. It activates the adhesive, ensuring a strong bond. It also provides uniform pressure, which is key for an even transfer of the design.
A heat press represents efficiency and reliability. It's essential for producing large volumes of high-quality prints quickly. This tool guarantees quality and supports rapid order fulfillment.
Understanding Direct-to-Film Printing
DTF printing is changing the game in product customization and design. A direct-to-film printer precisely prints designs onto clear film. This digital process captures complex designs in vibrant colors.
After printing, the next crucial step involves hot melt powder. The printer or operator evenly sprinkles this powder over the printed film, where it adheres to the wet ink.
Applying the right amount of hot melt powder evenly is critical. It ensures that the design will transfer well and endure over time. Once the operator applies the powder, they move the film to a curing or drying phase, preparing it for the heat press.
Hot melt powder plays a pivotal role in DTF printing. When heated, it activates, forming a durable bond between the film and the product. This bond is what makes the print long-lasting and of high quality.
The Heat Press Machine: A Closer Look
A heat press machine applies heat and pressure over a set period. This process is crucial for activating the hot melt powder on a DTF print, ensuring the design adheres firmly to the product. The machine's even heat distribution and adjustable pressure settings are key for a successful transfer, guaranteeing that each product comes out with a high-quality print.
Heat press machines are versatile, accommodating various product sizes and materials. They ensure that the hot melt powder melts and bonds the design to the product without damaging the product itself. This balance of heat and pressure is crucial for maintaining the integrity and appearance of both the design and the product.
There are several types of heat press machines suitable for DTF printing, each with its unique features.
Clamshell Heat Presses
These machines open and close like a clamshell. They are compact and easy to use, making them ideal for businesses with limited space. Clamshell presses are great for flat products but may not be the best choice for thicker items.
Swing-Away Heat Presses
Swing-away models have a top platen that swings away from the lower platen, providing better access to the printing area. This design minimizes the risk of contact with heated plates. It is safer and more suitable for products of varying thicknesses.
Drawer-Type Heat Presses
These machines feature a drawer that pulls out for a safe and easy layout of the product and film. They offer a good balance of safety and convenience, especially for high-volume operations.
Pneumatic Heat Presses
Pneumatic models use air pressure to achieve uniform pressure across the print surface, ideal for high-quality DTF prints. They are more expensive but offer precision and consistency, crucial for businesses focusing on quality.
Automatic Heat Presses
Automatic presses provide consistency with minimal manual intervention, perfect for large-scale operations. They can save time and labor, significantly increasing production efficiency.
Printing Process: Setting the Stage for Success
The pre-printing process in DTF printing is crucial for ensuring the final product meets high-quality standards. This stage involves several key steps, from preparing the design to ensuring the printer and materials are correctly set up for optimal results.
Step 1: Design Preparation
Begin by selecting a high-resolution design suitable for your product. The design's quality directly impacts the final print, so choose or create clear, vibrant images.
Use software to reverse (mirror) the image and adjust colors, if necessary, to ensure the design looks correct when transferred.
Step 2: Printer Setup
Select a DTF-specific film that will hold the ink and powder. The quality of the film affects the transfer's durability and clarity.
Fill your printer with DTF-specific inks, which are formulated to work with the hot melt powder and ensure vibrant, lasting colors.
Adjust the printer settings for the specific type of film and ink you're using. This includes resolution, color management, and print speed settings to optimize print quality.
Step 3: Printing the Design
Send your prepared design to the printer. Ensure the environment is dust-free to avoid imperfections. Immediately after printing, evenly distribute hot melt powder over the wet ink. The powder should cover all the ink to ensure proper adhesion during the heat press process.
Step 4: Curing the Print
Use a curing oven or a heat press set at a low temperature to melt the powder slightly and remove any excess. This step solidifies the powder's grip on the ink, preparing it for the final heat press.
The combination of heat and pressure ensures the melted powder thoroughly bonds the design to the product. It's crucial to set the heat press at the right temperature and pressure to achieve a strong, even bond without damaging the product or the design.
Preventing Material Wrinkles
Achieving smooth, wrinkle-free transfers is crucial in the DTF printing process, especially when aiming for high-quality results. Wrinkles in the transfer material can lead to imperfections in the final product, affecting both the visual appeal and the durability of the print.
Storing DTF films correctly is crucial to preventing them from curling or bending, which can introduce wrinkles. It's important to keep these films flat and in a low-humidity environment. Humidity can make the films warp or become sticky, which complicates the transfer process and can result in a less-than-perfect final product.
Before applying the transfer, pre-pressing the substrate (the item you're transferring onto) can remove any existing moisture and wrinkles.
This step involves placing the substrate in the heat press for a few seconds without the transfer film. Pre-pressing flattens the substrate, ensuring it's completely smooth and ready for transfer.
Carefully align and place the transfer film on the substrate. Misalignment can cause parts of the design to stretch or distort, leading to an uneven surface that may introduce wrinkles. Ensuring the film is correctly positioned also helps in achieving a uniform transfer without any creases or folds.
The heat press settings play a significant role in preventing wrinkles. Setting the correct temperature and pressure ensures the hot melt powder melts evenly, and the design transfers smoothly onto the substrate.
Too much pressure can squeeze out the adhesive, causing wrinkles, while insufficient heat may not activate the adhesive properly, leading to a weak bond that can crease or wrinkle over time.
Optimizing Heat Press Use for Wholesale Success
The cornerstone of wholesale success is the ability to deliver consistently high-quality products. This means paying close attention to the heat press settings for each type of product you print. The right combination of temperature, pressure, and time is essential to activate the hot melt powder correctly and achieve a durable bond without compromising the material or the print quality.
Optimizing the use of the heat press in a wholesale DTF printing operation involves a delicate balance of:
- Quality
- Speed
- Volume management
By focusing on consistent quality, balancing speed with quality, handling volumes efficiently, and ensuring the team has the right training and expertise, you can leverage your heat press setup for maximum success in the competitive wholesale market.
Empowering Your Business With Direct-to-Film Printer Technology
Heat press in conjunction with a direct-to-film printer is indispensable in achieving high-quality, durable prints for the wholesale market. This powerful duo enables businesses to produce vibrant, detailed designs.
At DTF Transfers Wholesale, we specialize in elevating your printing capabilities with top-notch DTF transfer services. Our commitment to quality, combined with cutting-edge technology and a dedicated team, guarantees that your designs translate flawlessly from vision to product.
Discover the difference with DTF Transfers Wholesale.
Leave a comment